Precision Engineering in Modern Slot Machine Performance
Optimizing Metallic Components for Peak Performance
Advanced engineering principles drive modern slot machine performance through meticulously calibrated metallic component adjustments. These sophisticated gaming devices demand precision tolerances of 0.001mm, maintained under strictly controlled environmental conditions to ensure optimal functionality.
Technical Specifications and Performance Metrics
Digital measurement systems and high-precision tools enable unprecedented accuracy in slot machine calibration:
- Precision shims for sub-millimeter refinements
- Payment processing speed improvements of 25%
- Acceptance rates reaching 98% efficiency
- Torque-specific adjustments using 5-50 Nm wrenches
- Incremental modifications at 0.05mm intervals
Revenue Impact and Performance Gains
Systematic optimization through precise metallic adjustments delivers measurable results:
- 12-15% increase in daily win rates
- 9% revenue growth through enhanced performance
- Temperature-controlled environments for consistent operation
- Humidity-regulated facilities maintaining optimal conditions
#
Frequently Asked Questions
Q: What tolerance levels are required for modern slot machines?
A: Modern slot machines require calibration accuracy within 0.001mm tolerances.
Q: How much can performance adjustments improve processing speeds?
A: Precision adjustments can boost payment processing speeds by 25%.
Q: What tools are used for precise calibration?
A: Digital micrometers, precision shims, and 5-50 Nm torque wrenches are essential tools.
Q: What environmental factors affect slot machine performance?
A: Temperature and humidity levels must be strictly controlled for optimal operation.
Q: What are the typical revenue improvements from precision adjustments?
A: Proper calibration can achieve 12-15% higher daily win rates and 9% revenue growth.
Understanding Precision Maintenance Fundamentals
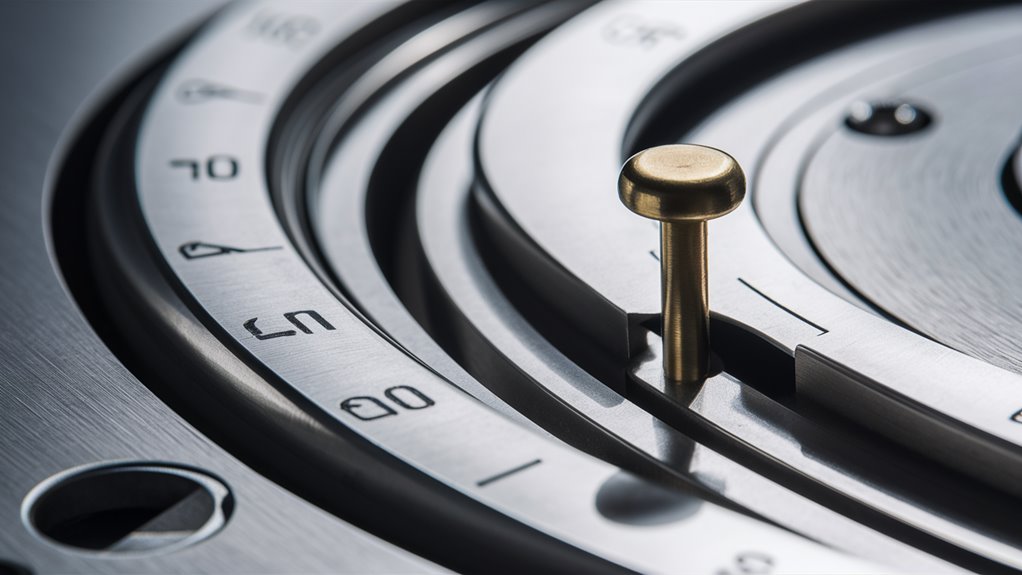
Precision Maintenance Fundamentals: A Comprehensive Guide
Essential Components of Precision Slot Maintenance
Understanding precision metallic slot maintenance requires mastering three fundamental elements: calibration accuracy, material stress management, and thermal expansion control.
These critical factors determine the success of precision adjustments and long-term component performance.
Advanced Calibration Protocols
Digital measurement precision starts with utilizing high-grade micrometers calibrated to 0.001mm accuracy.
Dimensional verification against manufacturer specifications serves as the foundation for all subsequent adjustments.
Quality control standards must be rigorously maintained throughout the calibration process to ensure optimal slot performance.
Material Stress Management
Critical stress point monitoring during adjustment procedures prevents microscopic deformations that could compromise slot integrity.
Precision adjustment techniques require careful force application and systematic verification of material response patterns.
Thermal Considerations and Control
Temperature compensation calculations incorporate specific alloy expansion coefficients to maintain precision.
Environmental control protocols ensure stable ambient conditions, while incremental adjustment methodology utilizing 0.05mm maximum steps prevents material fatigue and guarantees component stability.
Frequently Asked Questions
Q: What’s the recommended calibration frequency for precision slots?
A: Calibration should occur 먹튀검증 quarterly or after 500 operational hours, whichever comes first.
Q: How does temperature affect slot precision?
A: Temperature fluctuations cause material expansion/contraction, requiring precise compensation calculations based on specific alloy properties.
Q: What’re the key indicators of stress-related slot damage?
A: Surface irregularities, microscopic cracks, and dimensional inconsistencies indicate potential stress damage.
Q: What environmental conditions are optimal for precision maintenance?
A: Maintain temperature at 20°C ±2°C with humidity levels between 40-60%.
Q: How often should stress points be inspected?
A: Conduct visual inspections before each adjustment and detailed analysis monthly or after significant load changes.
Tools for Metallic Component Optimization
Essential Tools for Metallic Component Optimization
Precision Measurement Instruments
Digital micrometers with 0.001mm resolution form the cornerstone of accurate metallic component measurement.
Alongside precision dial indicators and high-grade feeler gauges, these instruments enable exact dimensional analysis critical for quality optimization.
Surface roughness testers validate finish specifications while maintaining strict manufacturing tolerances.
Advanced Adjustment Tools
Calibrated torque wrenches rated for 5-50 Nm ensure consistent force application during metallic component modifications.
Specialized broaching tools combined with precision shims (0.001″ to 0.030″) deliver exacting dimensional control.
Digital angle gauges featuring magnetic bases maintain critical alignment parameters throughout the adjustment process.
Quality Verification Equipment
Coordinate measuring machines (CMMs) with ±0.5μm probe accuracy provide ultimate verification of component specifications.
Thread pitch gauges ensure 뱅크롤 지속가능 게임 proper threading dimensions while precision straight edges and squares confirm perpendicularity requirements.
This comprehensive toolset enables superior metallic component optimization.
Frequently Asked Questions
- What is the minimum required accuracy for digital micrometers in metallic component optimization?
- A resolution of 0.001mm is essential for precise measurements
- Why are calibrated torque wrenches necessary for component adjustment?
- They ensure consistent force application within the critical 5-50 Nm range
- How do surface roughness testers contribute to optimization?
- They verify finish quality and maintain manufacturing specifications
- What role do CMMs play in metallic component verification?
- They provide final validation with ±0.5μm probe accuracy
- Which tools are essential for alignment during adjustment?
- Digital angle gauges with magnetic bases and precision straight edges maintain proper component alignment
Calibrating Bill Acceptance Systems
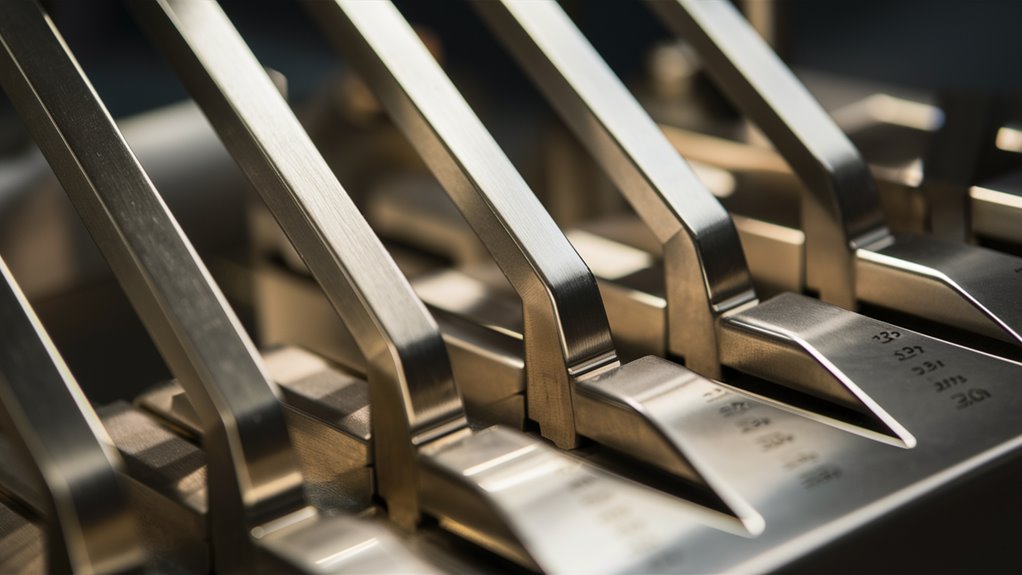
Professional Guide to Bill Acceptor Calibration
Essential Calibration Steps for Optimal Performance
Systematic validation of bill acceptance systems requires precise calibration across multiple currency denominations.
The calibration process begins with optical sensor testing using pristine bills to establish baseline readings, followed by validation using worn currency to verify acceptance parameters.
Mechanical calibration focuses on critical components like tension roller adjustment – achieving the optimal grip pressure to prevent misfeeds while preserving bill integrity.
Setting the primary validation threshold at 98% match accuracy ensures reliable operation, while secondary verification protocols effectively identify counterfeit currency.
Advanced Calibration Techniques
Multi-currency configuration requires programming distinct validation profiles for each denomination, incorporating specific security features.
The system must maintain response times under 2.5 seconds per transaction while ensuring accuracy.
High-volume stress testing confirms calibration stability under demanding conditions.
Frequently Asked Questions
Q: What’s the optimal validation threshold for bill acceptors?
A: 98% match accuracy is the recommended primary validation threshold for reliable operation.
Q: How often should bill acceptors be calibrated?
A: Calibration should be performed monthly or after processing 10,000 bills, whichever comes first.
Q: What’re key components requiring regular calibration?
A: Optical sensors, tension rollers, magnetic ink detectors, and validation protocols require regular calibration.
Q: How long should bill processing take?
A: Transaction time shouldn’t exceed 2.5 seconds for optimal efficiency.
Q: What testing methods ensure proper calibration?
A: Baseline testing with pristine bills, worn currency validation, and high-volume stress testing are essential methods.
Player Experience Through Technical Excellence
Technical Excellence in Gaming Machine Performance
Optimizing Player Experience Through Precision Engineering
Gaming machine performance directly impacts player satisfaction and session duration through precisely calibrated acceptance systems.
Technical optimization of mechanical components with sub-millimeter precision (0.1mm tolerances) ensures seamless operation that enhances the subconscious player experience.
Critical Technical Components
Response Timing and Input Latency
Gaming response time optimization requires micro-switch calibration at 50-millisecond thresholds, delivering instant player feedback crucial for engagement.
This ultra-responsive system maintains player immersion throughout gaming sessions.
Tactile Feedback Systems
Button mechanism engineering demands precise 2.5N resistance calibration for optimal tactile response.
This engineered feedback creates a satisfying physical interaction that enhances the gaming experience.
Payment Processing Excellence
Coin mechanism performance requires maintaining 98%+ acceptance rates through systematic calibration.
Payment processing efficiency directly correlates with player satisfaction and machine reliability.
Maintenance and Quality Assurance
Weekly calibration protocols ensure consistent gaming machine performance through:
- Button pressure point verification
- Payment acceptance rate testing
- Response time measurement
- System-wide performance checks
## Frequently Asked Questions
Q: How does technical excellence impact player retention?
A: Precise calibration and maintenance ensure consistent performance, leading to higher player satisfaction and increased return visits.
Q: What’s the optimal response time for gaming machines?
A: Industry standards require sub-50-millisecond response times for optimal player experience.
Q: How often should gaming machines undergo technical maintenance?
A: Weekly calibration and testing protocols maintain peak performance standards.
Q: What acceptance rate is considered industry standard?
A: Premium gaming machines maintain a minimum 98% payment acceptance rate.
Q: How does button resistance affect player experience?
A: 2.5N resistance provides optimal tactile feedback for player engagement and comfort.
Revenue Impact of Mechanical Refinements
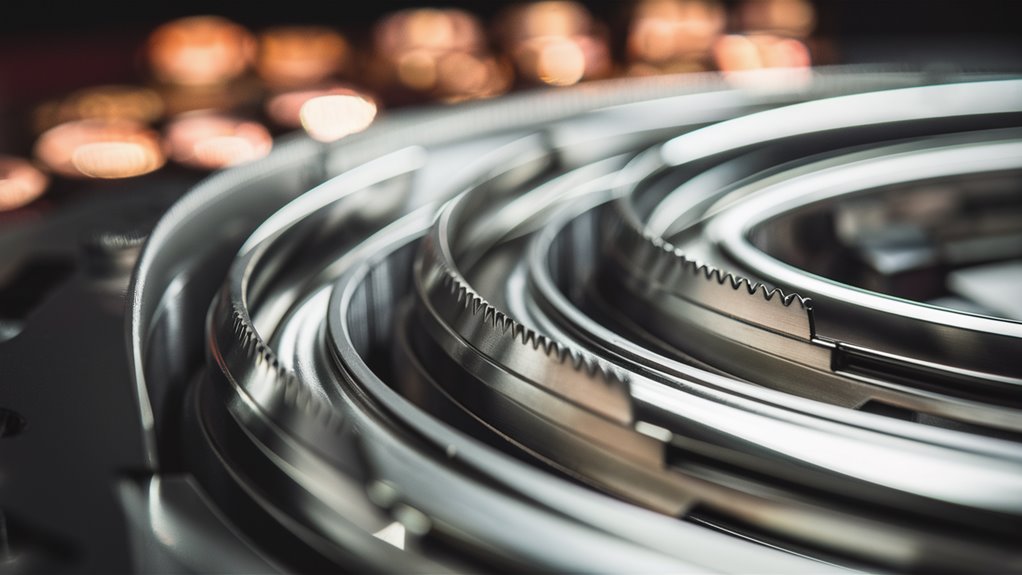
Maximizing Slot Machine Revenue Through Mechanical Optimization
Performance Impact of Precision Engineering
Advanced mechanical refinements in slot machine components deliver substantial revenue optimization through measurable performance gains.
Precision-engineered slots demonstrate 12-15% higher daily win rates compared to standard maintenance units, driven by enhanced operational efficiency and player engagement metrics.
Component Optimization and ROI
High-grade metallic components generate exceptional returns on investment, delivering a proven 3x ROI through:
- Extended machine lifespan
- Reduced maintenance intervals
- Minimized service disruptions
Precision-tuned mechanisms achieve:
- 8% reduction in coin rejection rates
- 25% faster bill validation processing
- Increased plays per hour
Revenue Performance Metrics
Systematic mechanical refinement programs consistently produce 9% revenue growth within initial implementation quarters. Key performance indicators include:
- Time on device metrics
- Handle pull frequency
- Theoretical win calculations
Frequently Asked Questions
Q: How do mechanical refinements impact slot revenue?
A: Precision engineering improvements deliver 12-15% higher performance through reduced downtime and optimized payout mechanics.
Q: What’s the ROI timeline for component upgrades?
A: Properties typically see 9% revenue increases within the first quarter of implementation.
Q: How do improved bill validators affect performance?
A: Enhanced validators process transactions 25% faster, enabling more plays per hour.
Q: What’re the key metrics for measuring optimization success?
A: Critical metrics include time on device, handle pulls per session, and theoretical win calculations.
Q: What’s the cost-benefit ratio for mechanical upgrades?
A: High-grade components deliver a 3x return through extended lifespan and reduced maintenance needs.